煤传媒03-15

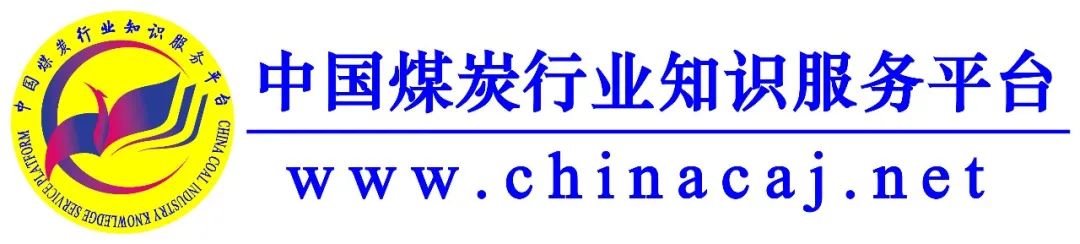
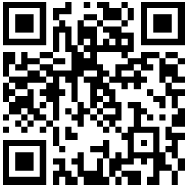
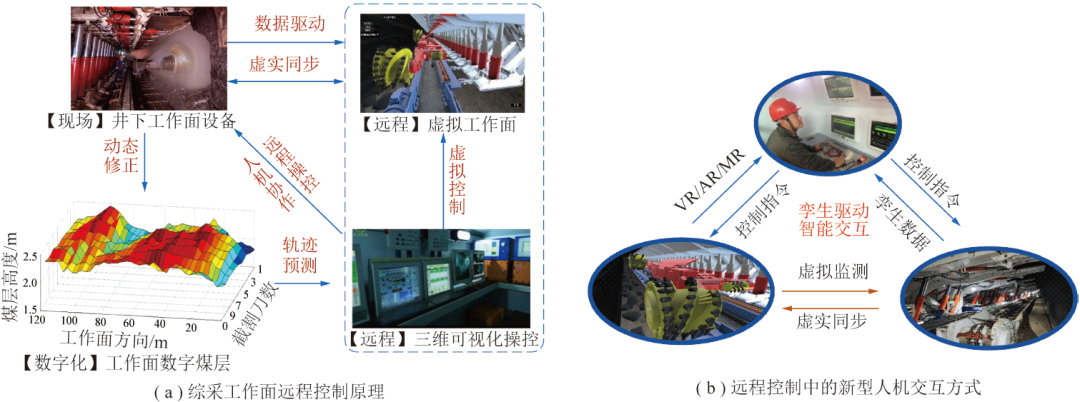
相比于综采工作面,目前绝大多数巷道掘进采用的悬臂式掘进机施工尚采用人工操作,施工时掘进机司机通过目视断面上的激光光斑控制掘进机截割头,巷道中心轴线靠精确调整的激光指向仪设定激光光斑保证,掘进工程质量很大程度上取决于司机的经验和熟练程度。考虑掘进工作面工况存在的高粉尘、低照度、复杂地质条件等因素,现有掘进质量规范下掘进装备的位姿和工况状态检测难度极大,表现在:成形截割精度要求高(安全规程要求小于100mm),机身和截割头位姿测量精度直接影响巷道成形断面误差,定向精度导致的巷道开拓误差对后继施工影响较大等。因此,煤矿井下掘进装备的动态、精确定位技术已经成为提升采掘效率,解决“采掘失衡”难题的行业共识。
远程掘进应该包含本地控制和远程控制内容,前者是后者的依托和基础。井下巷道掘进设备的姿态精确测量、自主定位与导航、掘进断面自动成形监控,以及人员定位与防护、锚固作业自动化、掘-支-运设备自主联动、掘进过程可视化监测和实时通信都是远程掘进需要解决的问题。如图下图所示,设备精确位姿测量解决“在哪里”的问题,最为关键;其次自主定位与导航解决“去哪里”的问题,关系到掘进方向是否正确,也是巷道截割质量评价的关键,需要设备群的协同。
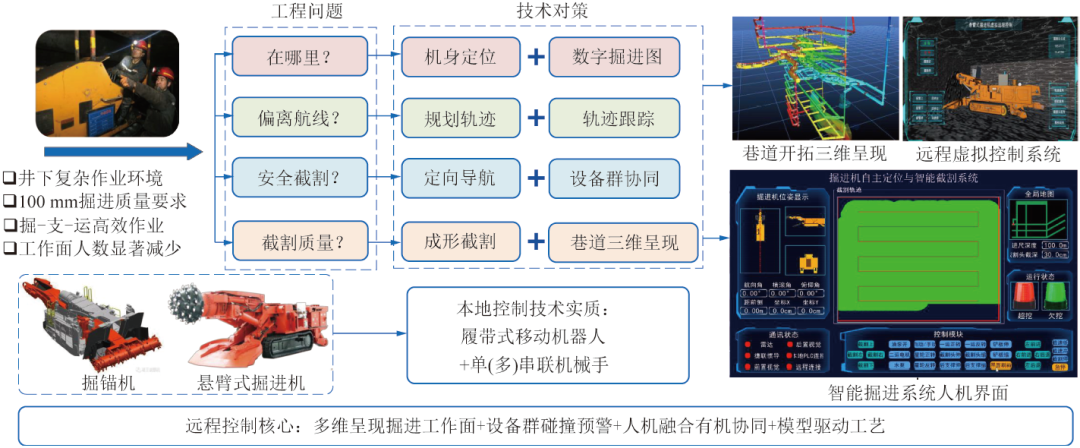
煤矿井下巷道掘进本地控制的实质是将掘进设备作为“移动机器人+串联机械手”组合体,利用机器人正、逆运动学求解,以设计路径参数为目标,以实时测量数据为反馈,达到伺服控制、轨迹跟踪的结果,形成要求的形状和尺寸的高质量巷道。解决了上述井下问题,在掘进工作面远端或地面远程控制时,除了关注井下工作面设备工况和控制状态,需要解决数据直观呈现的问题,为监控人员提供更多决策信息能够在自动作业过程中对异常状态进行人为干预,达到“人机协同”远程掘进控制的目的。因此,提升井下掘进机智能化水平,以机器人技术、数字工作面、精确定位、自主导航、定形截割构建本地控制理论和技术基础,解决远程控制中的多维数据呈现、设备群碰撞、掘进工艺建模和人机协同机制问题,是远程智能掘进的关键。
针对煤矿井下采煤和掘进施工复杂度高、监测数据量大,协同控制难度大,“自动控制+人工视频干预”的控制方案难以实现工作面常态化自动生产等问题, 近几年煤炭行业多家研究单位将数字孪生(DT)和虚拟现实(VR)引入采掘工作面设备群远程智能控制决策系统,提出“惯导+”或“视觉+”等多种方法有效解决煤矿井下采掘工作面设备精确定位、自主导航和自主截割难题,“数字煤层、虚实同步、数据驱动、实时修正、虚拟碰撞、截割预测、人机协同”的煤矿井下设备远程控制技术体系已经成为行业解决采掘工作面智能化的共识,这对破解目前煤矿井下工作面煤岩界面预测、少人或无人自动截割控制、设备群间异常检测等难题起到了重要推动作用。
在前期研究基础上,笔者提出了数字孪生驱动掘进装备远程智能控制技术构架,通过构建掘进工作面数字孪生体,将井下人员、设备、环境相关信息呈现到数字空间,虚实融合,共智互驱,达到数字掘进与物理掘进智能协同的目标,破解掘进施工中人-机-环共生安全难题。为了聚焦远程控制任务,提出以掘进为控制时空参考的掘-支-运作业机制,以掘进定位、定向导航和定形截割为核心,自动钻锚和高效转运辅助的远程控制构架。下面两图分别为数字孪生驱动掘进装备远程控制模型及技术体系示意、远程智能掘进的系统架构。
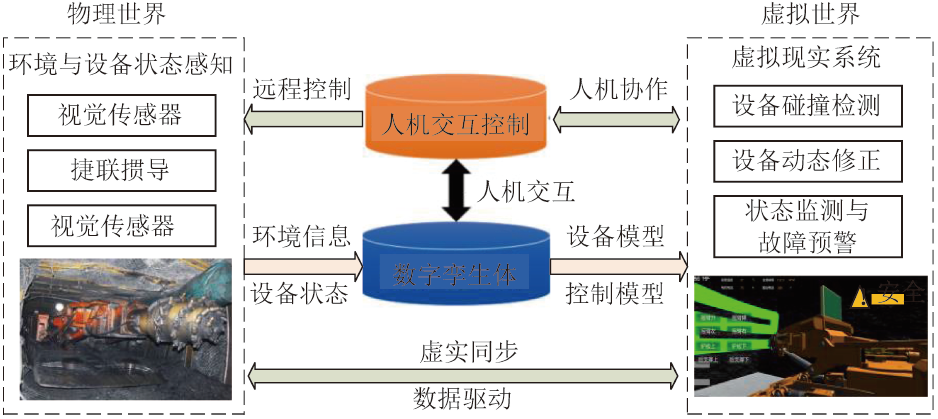
数字孪生驱动掘进装备远程智能控制模型及技术体系

该远程控制系统主要功能:
(1)基于激光点-线特征的掘进机机身和截割臂视觉测量,获得井下巷道掘进设备移动中的精确位姿(包括位置和姿态)和截割臂实时位姿数据,结合掘进机参数解算出截割头的运动轨迹。
(2)利用(1)的结果,实现人工示教轨迹规划,破解复杂工况和环境下的掘进机轨迹规划难题,即熟练司机操作机身和截割臂完成一个截割循环,实时记录位姿信息数据,下一个截割循环采用记忆数据控制掘进全过程中的机身和截割臂运动,实现自动化截割、自动刷帮等工艺环节。
(3)以巷道、掘-支-运设备群等静态信息,加上掘进中的巷道动态变化和设备实时位姿等数据,建立设备位姿显示、运动学、协调控制、自主决策等方面的数学模型,构建掘进工作面人-机-环数字孪生体。
(4)掘进监控中,以物理世界——井下掘进工作面设备群实时数据,驱动虚拟世界——掘进工作面孪生体,实现虚实同步运动和虚拟设备群位姿实时修正,从而保证虚拟空间呈现场景可以作为远程控制的决策依据。
掘进工作面智能化的研究不断深入,近几年已经成为煤矿智能化研究的热点,但是在相关基础理论、设备定位、定向导航与纠偏、成形截割、协同控制等方面还存在不足。
(1)掘进状态感知基础理论研究不足
掘进工作面设备定向与定形截割、设备群碰撞预警与协同控制,都受制于位姿测量的准确性和可靠性。针对掘进机的精确位姿测量问题,国内外众多高校、研究机构开展了卓有成效的研究。目前掘进机的自动位姿测量方法中全站仪导向技术对环境要求较高,惯性导航技术定位时间累积误差大,罗盘类传感器精度易受外界电磁干扰,视觉测量要克服井下恶劣工作环境以及相机拍摄姿态等方面影响。视觉测量技术由于非接触、无累计误差等优势得到广泛关注,也在掘进机位姿测量方面得到一定程度的应用。但是掘进巷道工况环境恶劣,粉尘质量浓度高、伴随有水雾、杂光干扰,以及采掘振动影响等因素对图像测量的稳定性和可靠性影响很大。因此,如何实现综掘工作面复杂工作环境中掘进机的精准定位、高效开采活动成为了矿山工程领域发展过程中面临的科学难题。
悬臂式掘进机的定向掘进是解决巷道掘进方向控制的关键问题。巷道施工中根据位姿误差信息对机身进行控制,连续的航向位姿形成定向导航实际路径,结合截割臂的运动控制可以实现巷道断面的成形控制。非全断面掘进设备需要控制机身和截割头,实现预定截割轨迹的跟踪控制,全断面掘进设备相对简单,仅需关注航向方向位移为掘进进尺提供参考。由于悬臂式掘进机掘进使用最广、最灵活,但工艺复杂、一般使用在地质复杂场合,因此,国内外对其成形截割控制研究较多。现有研究对重载非完整约束的悬臂式掘进机器人开展较多,思路是将截割臂当做一个移动机械臂,进行统一的运动学建模实现掘进机的机器人化,实现悬臂式掘进机自动截割。但是由于机身位姿测量的成本和技术限制,基于机身位姿测量数据和规划轨迹的全局轨迹(包括机身轨迹和截割头轨迹2部分)跟踪控制还处于研究阶段。
智能协同控制技术是智能掘进机器人系统的核心。掘进工作面实现掘-锚-支-运-通过程中,设备群协同是实现多工序并行作业的技术基础。在实现单个设备智能控制的基础上,如何通过对煤矿掘进多个任务并行、多个设备智能协同控制成为重要研究内容之一。目前,掘进工作面作业线上各设备独立,缺乏信息感知、交流、互通功能,实时协作能力弱、人机交互性差,掘进工艺流程缺乏统一规范,要实现巷道智能化快速掘进,就必须建立掘进设备各子系统之间的并行协同控制机制。
我国煤矿赋存条件复杂,掘进工作面环境恶劣,存在煤层起伏大、顶板松软、夹矸与片帮并存、水与瓦斯突出等一系列问题,且不同矿区差异大,掘进作业本地控制的自动化、智能化难度较大。虽然地面一键启动、数据驱动远程监控、三维可视化监测等技术得到一定应用,但是对井下采掘工作面的远程控制基础理论和技术研究基本处于空白,行业还存在“快”即为实时,控制没有模型的理解误区。因此,煤矿网络控制系统实时性保障技术、网络通信系统实时性、数字孪生驱动的远程掘进控制系统模型等基础理论及技术研究应该高度重视,这是实现真正意义上的远程控制必经之路。
(1)“DT+VR”井下掘进人-机-环智能管控技术
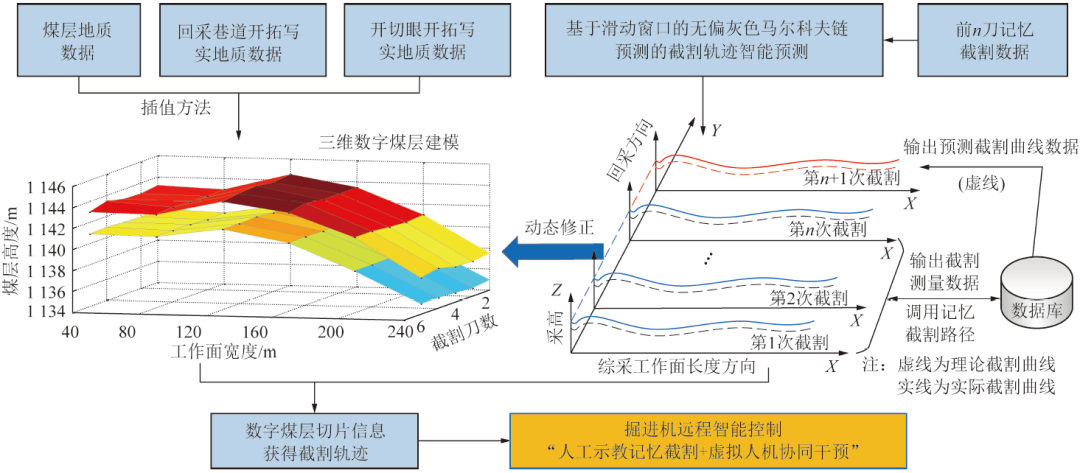
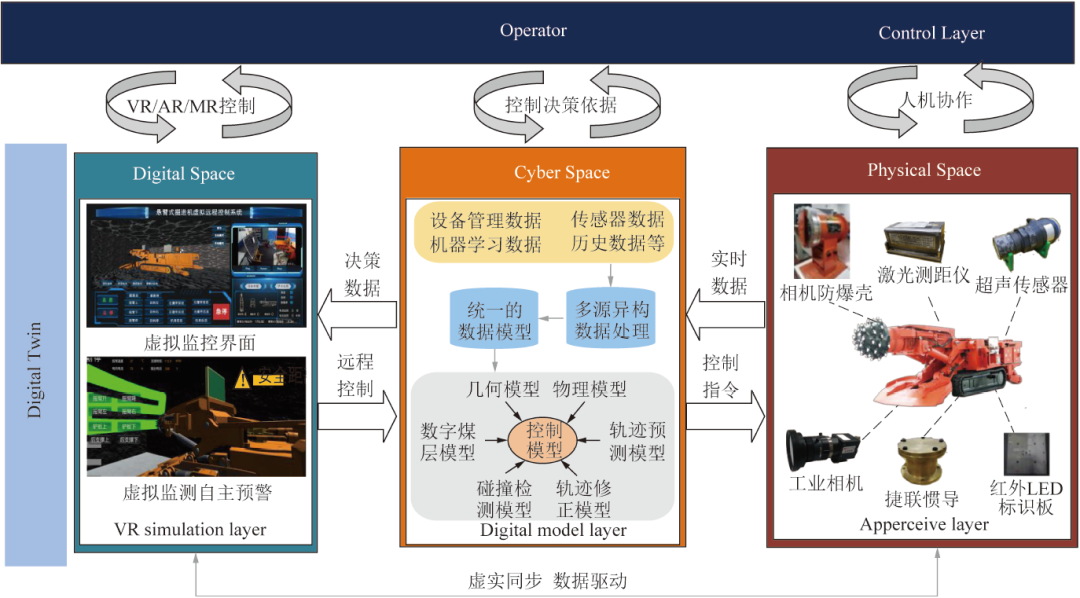
②煤矿井下视觉成像系统标定基础理论。近年来,智能视觉技术在煤矿井下迅猛发展,在固定设备及场合视觉监测、煤流检测、人员定位及异常状态识别,甚至工作面直线度和设备位姿测量方面得到一定的工程应用。但是影响图像质量的防爆玻璃折射、采掘振动影响,以及高粉尘、低照度和杂光干扰环境下的应用性研究基本空白,影响了测量的稳定性和精度。
悬臂式掘进机机身及截割头位姿的实时、准确测量是实现煤矿巷道掘进定向导航和定形截割的基础和核心内容。针对掘进机的自动位姿测量技术方面的研究,专家学者们提出了多种不同的技术方案,并取得了一定的研究成果。目前方法主要有iGPS测量技术、基于全站仪的导向和定位、惯性测量技术、超宽带测量技术、空间交汇测量技术和视觉测量等。基于全站仪的测量系统由于掘进过程中巷道内粉尘质量浓度大,测量环境恶劣,加之棱镜光路易遮挡,测量结果稳定性亟待解决。基于惯性传感器的掘进机位姿测量系统存在时间累积误差,难以长程连续地提供位置参量,目前研究热点是如何将井下采掘与施工工艺有机结合解决工程难题。基于立体视觉的掘进机机身位姿检测技术,在矿井下的应用主要集中于对车辆与人员的监控,而应用于机身定位方面的文献较少。吴淼研究团队研究基于空间交汇测量技术的悬臂式掘进机位姿自主测量方法,得到悬臂式掘进机在固定坐标系下的位姿状态。西安科技大学近年来系统研究了煤矿井下移动目标的位姿测量问题,在采掘工作面智能化建设中得到一定程度的验证。

矿用图像模糊建模与去模糊
(3)定向导航与纠偏技术
煤矿井下掘进设备导航目前有基于惯性导航、惯导+组合导航方式、基于视觉导航方式、惯导+视觉组合方式。吴淼教授团队深入研究了掘进机导航系统,提出的二维里程辅助自主导航方法,分析掘进机滑移特点研制出一种外置式二维里程的测量装置,实现了二维里程辅助的组合导航算法。
在实现掘进机位姿检测的基础上,须完成掘进机的自主纠偏以保证巷道截割质量。针对工况复杂且存在封闭边界的受限巷道空间,吴淼等将综掘巷道环境自适应划分为区域栅格,提出掘进机纠偏影响度作为模型降维与简化的指标,结合掘进机自身运动特点与实际工况,建立掘进机在栅格场景中的自主纠偏运动模型,实现了结合PID算法与神经网络的自主纠偏算法,并采用EBZ-55掘进机与模拟巷道验证了纠偏算法的可行性。
吴淼团队多年坚持智能掘进技术研究,对自适应控制、记忆截割进行了很多有创意的探索。针对井下掘进机截割智能化程度低、截割臂摆速不能根据煤岩硬度进行自适应调节的问题,研究了基于多种传感器信息掘进机截割臂自适应截割控制策略和掘进机姿态调整模型辨识与精准控制方法;针对煤矿掘进机机器人化和无人化的目标,提出了一种悬臂式掘进机煤矸智能截割控制系统与方法,提高掘进机截割煤矸的效率和智能化程度;针对常见及复杂构造断面,提出了悬臂式掘进机断面成型轨迹多目标优化方法。
另外,为实现从人工截割到自主截割,吴淼课题组提出一种纵轴式掘进机记忆截割控制方法,如下图示,该方法可对人工示范的过程进行记忆学习及智能优化,并一键式触发掘进机按所学路径信息自动截割后续断面,还可根据实际截割情况对路径进行微调,以避开煤岩过硬的位置。地面试验结果表明,系统运行稳定可靠,控制精度较高。但是该方法未将机身运行考虑进截割头位姿跟踪环节,限制了使用效果。
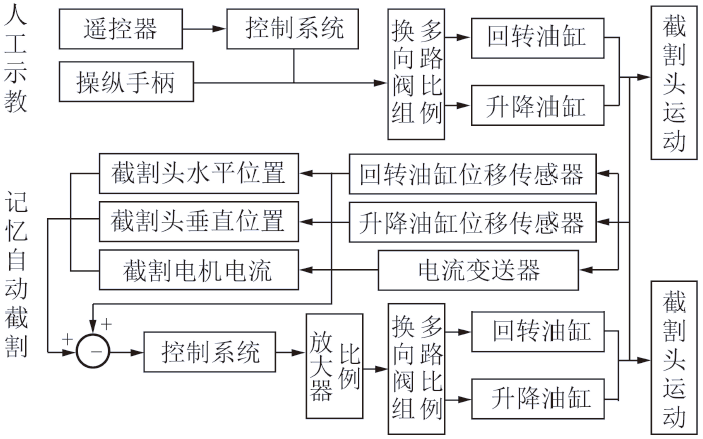
笔者所在课题组研究了悬臂式掘进机视觉伺服控制技术,提出采用视觉实时位姿测量和电液伺服控制,采用轨迹规划与人工示教相结合的方式,实现复杂运动环境下的掘进机机身视觉伺服和截割头运动轨迹跟踪控制。考虑不同地质条件和底板稳定性影响,先利用视觉位姿测量方法,实时记录人工操作机身和截割臂的轨迹完成一个截割循环,随后下一个截割循环采用记忆数据控制掘进全过程中的机身和截割臂运动,实现自动化截割、自动刷帮等工艺环节,避免了掘进机在不同工况和环境下的轨迹规划难题。下图为悬臂式掘进机的人工示教记忆截割控制系统原理框图。
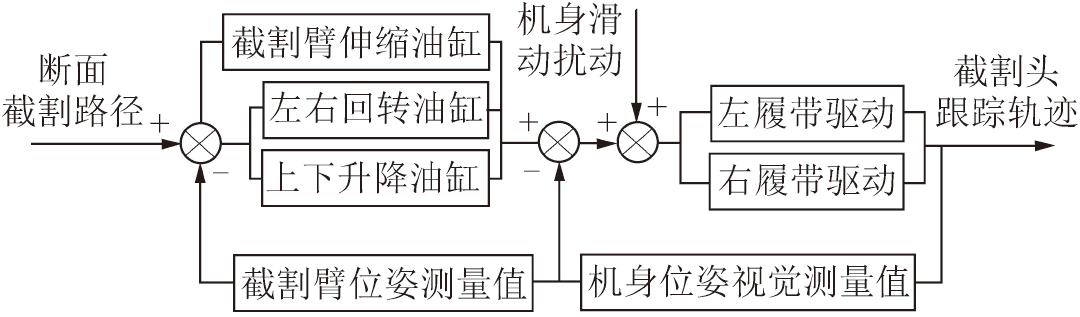
系统以截割头跟踪截割断面为目标,视觉实时测量的截割头位姿(包括截割头相对机身的位姿和机身位姿)为反馈量。为保证断面成形精度,基于截割头位置信息建立截割头轨迹跟踪控制模型,以截割头位姿为反馈确定截割头位置偏差,利用控制算法输出控制命令,使升降油缸及回转油缸驱动截割臂摆动工作,同时按照截割工艺要求调整机身位置,使之处于合理姿态并在截割轨迹跟踪时利用前铲板和后支腿固定机身。此技术的关键是掘进机机身的实时位姿测量,基于三激光束的视觉测量系统高精度、稳定性是其中的核心技术,最大优势是可以解决巷道断面形状、尺寸大小不同引起的截割路径自动规划困境,尤其是机身有滑动状态时机身控制难题。
按照掘-支-运工序并行提高掘进效率是目前行业努力的方向,通过建立掘进机群组位姿和运动关联模型,对多机群组的时空坐标系进行统一,在单机设备自动化的基础上进行多机群组的精准定位与智能导航,解决多机协同并行作业冲突的问题。多设备协同包括2方面:① 建立多个设备之间的空间位置关系,一般通过基坐标系标定来实现;② 协同插补算法,协同插补算法中的关键技术是协同轨迹的过渡和对多个运动单元的同步速度规划。
虚拟现实技术有助于解决多维信息空间的数据处理问题,建立人、设备、环境有机融合的多维空间,实现复杂或危险作业环境下的工业设备顺利作业。张旭辉等提出了一种“数字煤层、虚实同步、数据驱动、实时修正、虚拟碰撞、截割预测、人机协同”的煤矿井下设备远程控制技术体系。结合数字孪生和虚拟仿真等技术,提出面向煤矿井下装备智能控制的人-信息-物理系统HCPS 交互机制,实现掘进工作面物理空间与掘进信息虚拟空间的深度融合与交互。
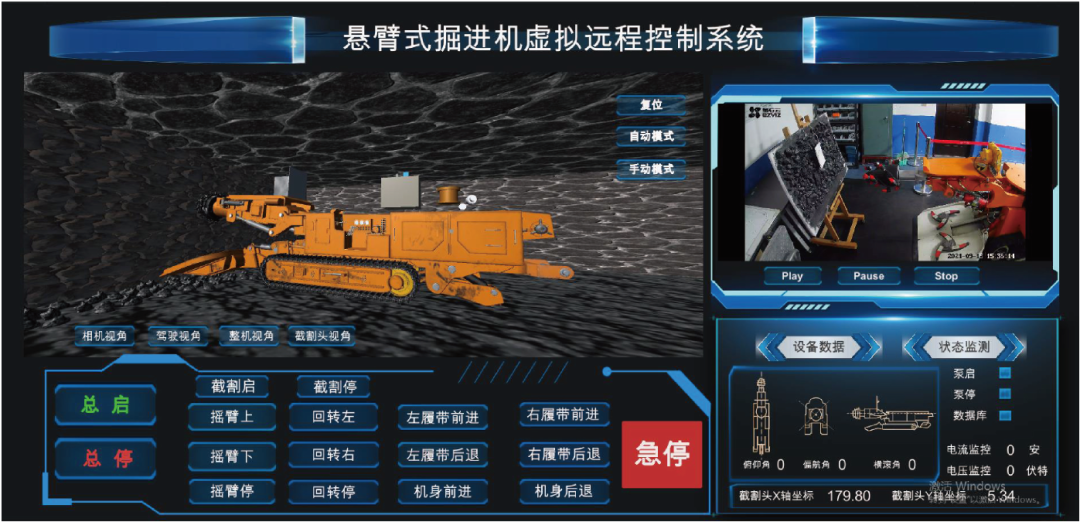
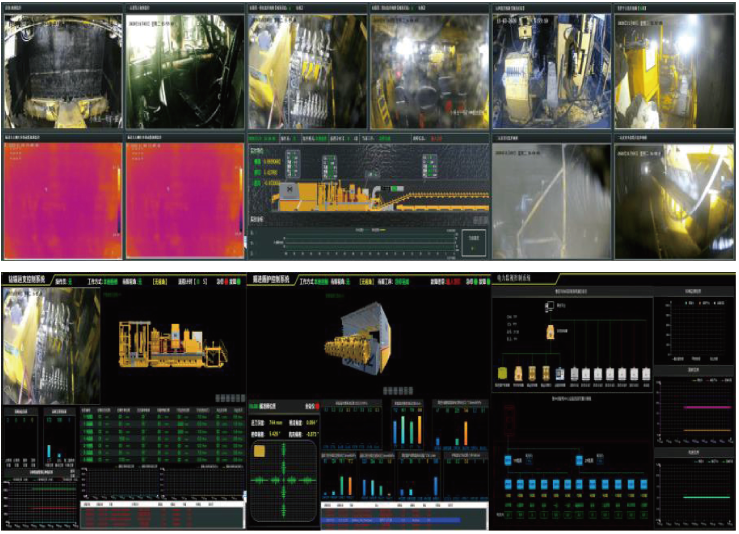
近几年工业通信网络在掘进工作面得到迅速发展和应用。通过部署矿用5G设备实现掘进巷道工作区域5G网络稳定覆盖,利用5G网络可实现掘进机运行状态、机载传感器、机载工业视频等数据传输至掘进工作面监控中心及地面调度信息中心,为掘进机远程控制解决了数据和视频传输方面的瓶颈。
但是许多网络协议导致的网络延迟是时变的,如DeviceNet、无线网络和Ethernet,作为远程控制系统通信通道时必须引起高度重视。具有控制功能的远程掘进系统本质上是典型的网络控制系统,应该考虑不同链路的监测数据和控制数据的差异,特别是为了满足控制性能要求和系统稳定性,需要对NCS采样周期进行正确的选择。
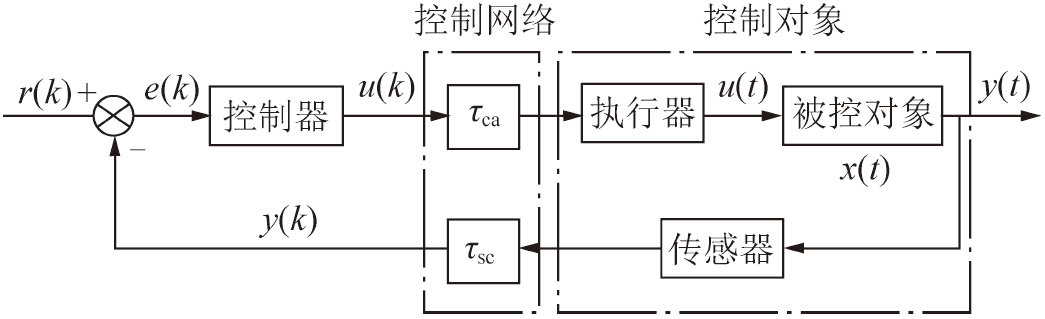
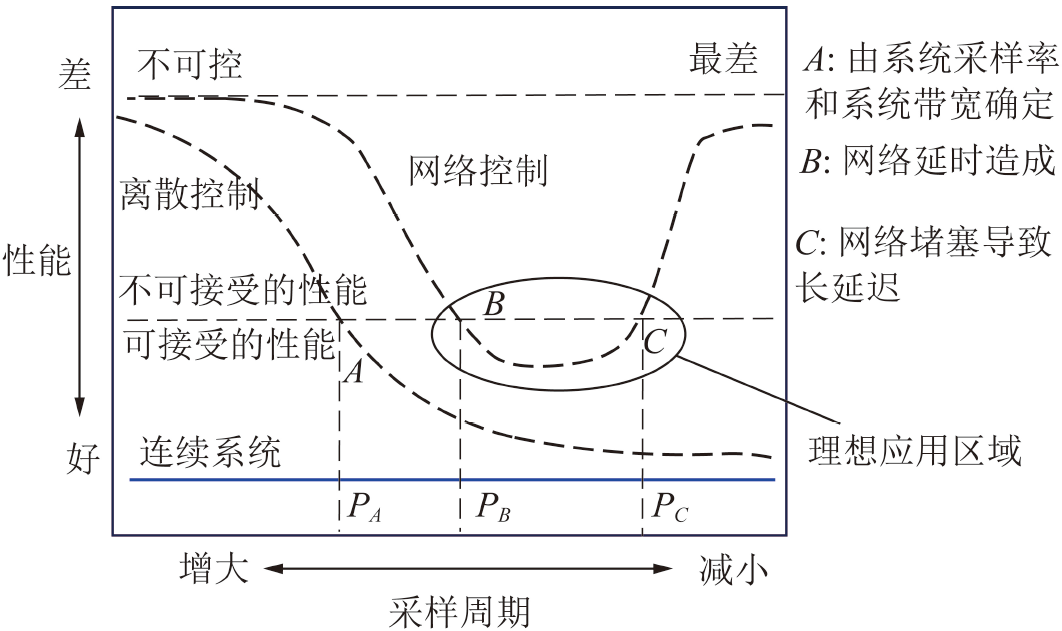
因此,在设计远程掘进控制系统时,必须针对控制器、传感器和执行器的特点研究网络时延对网络控制系统的影响,还要确定合理的采样速率和信息传递的时间间隔,以保证网络控制系统的性能和效率。
作者简介
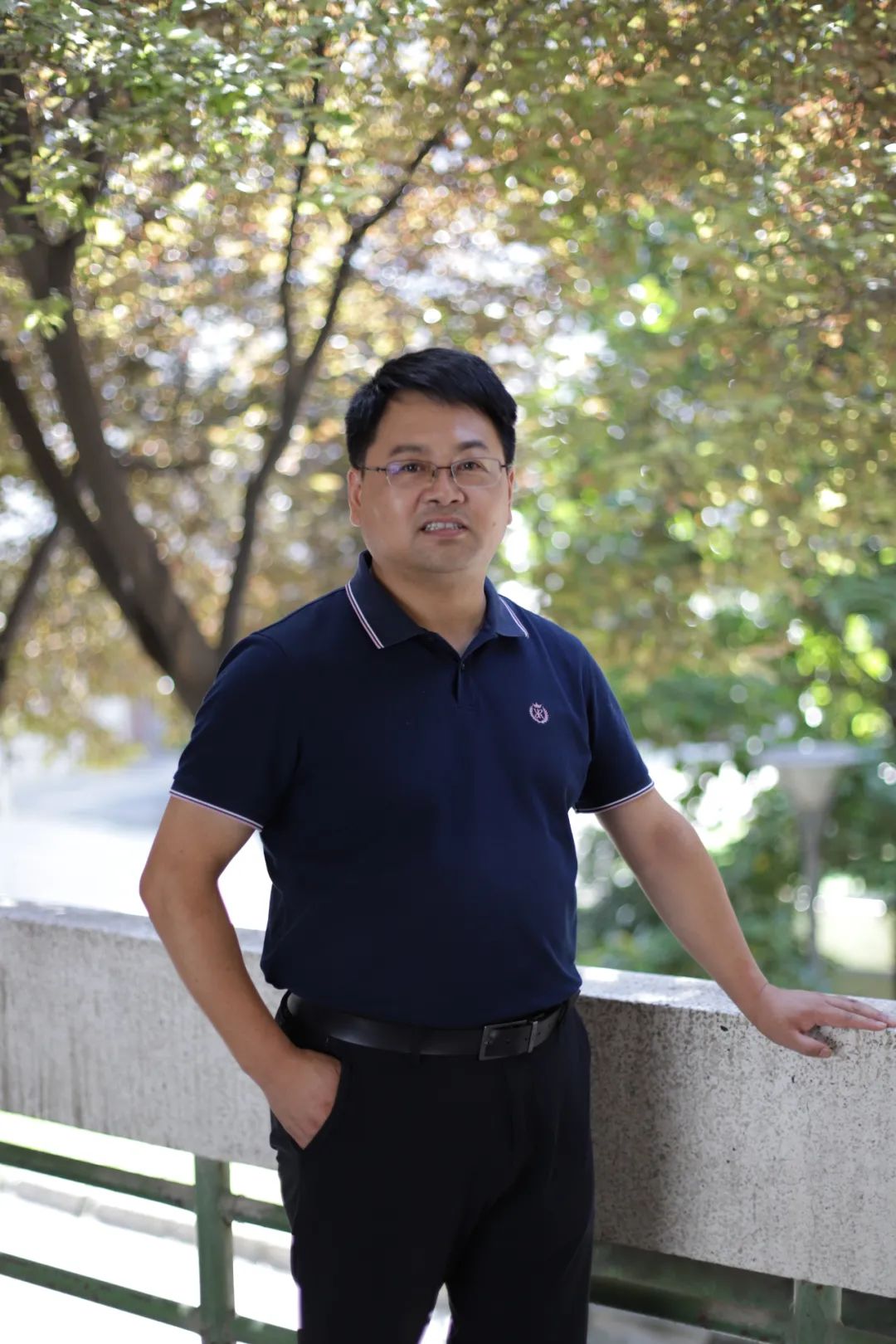
张旭辉,杨文娟,薛旭升,等. 煤矿远程智能掘进面临的挑战与研究进展[J]. 煤炭学报,2022,47(1):579-597.

文章来源:煤炭学报
尊重原创,如有侵权,请联系删除。
免责声明:以上内容转载自传煤,所发内容不代表本平台立场。
全国能源信息平台联系电话:010-65367702,邮箱:hz@people-energy.com.cn,地址:北京市朝阳区金台西路2号人民日报社